REFRACTORY SELECTION, MAINTENANCE AND RELATED DEFECTS (INTRODUCTORY TRAINING)
The refractory materials used in industrial melting furnaces are a huge investment for the glass manufacturer. Choosing the correct refractories is key to improving furnace lifetime, reducing energy costs, and minimizing refractory-related defects. The course will provide you with insight into why different parts of the furnace, including melter, refiner, working end, forehearth channels, and regenerator chambers, require different refractory types with specific chemistry and properties. The course will also provide you with some maintenance techniques that can be used to increase the furnace lifetime and reduce the risk of refractory failures.
Contents
• Key refractory materials, requirements and properties
• Interaction mechanisms of refractories in contact with the glass, the flue gases and each other
• Refractory testing and on-line monitoring techniques
• Preventive maintenance of the furnace structure
• Corrective maintenance and hot repair of the furnace structure
• Identify and understand refractory related solid defects and cords
• Exercises on:
– Refractory selection for different furnace parts
– Thermal insulation of refractory walls
– Refractory defect identification
– Technique for furnace maintenance
After the training you will
• Have an overview of chemistry and properties of refractory types for the different parts of furnaces and their purpose
• Understand the corrosion mechanisms of refractories in contact with the glass melt, in the superstructure/crown and in the regenerators
• Have knowledge of techniques to test, monitor and control the thickness of refractory walls
• Understand the defect types that can originate from different refractories in the furnace
• Have some techniques for preventive and corrective maintenance of the furnace structure
Training methods
We offer a blended learning approach by mixing e-learning, lectures, open discussions, exercises, and case studies in teams or individually. The number of participants per course is between 8 and 20 to maximize your learning experience. Participants always receive the presentations and a training certificate.
Level of seniority
This training is meant for junior professionals to skilled professionals seeking to deepen their knowledge.
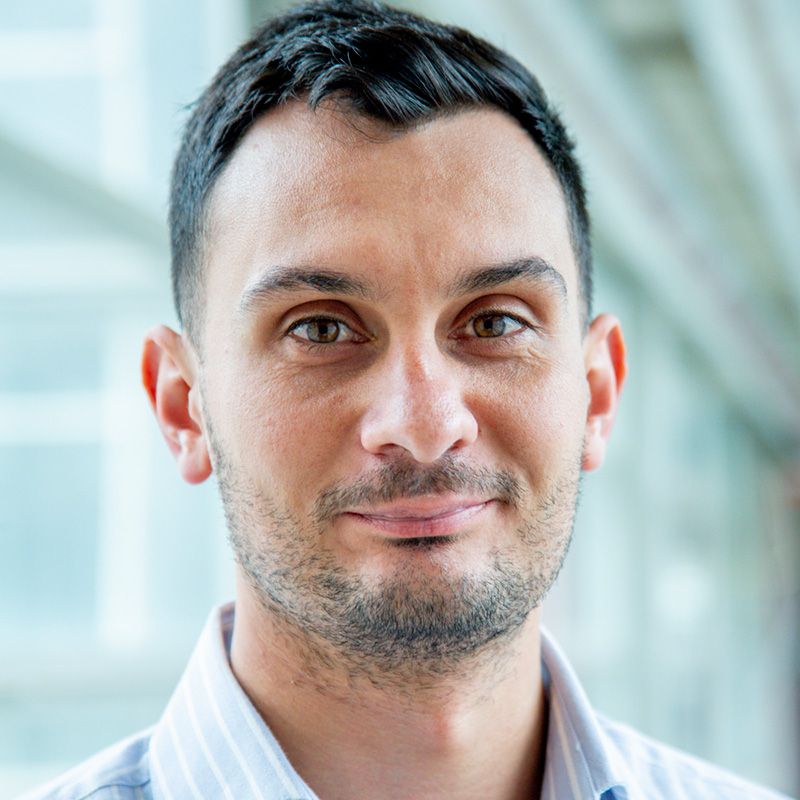
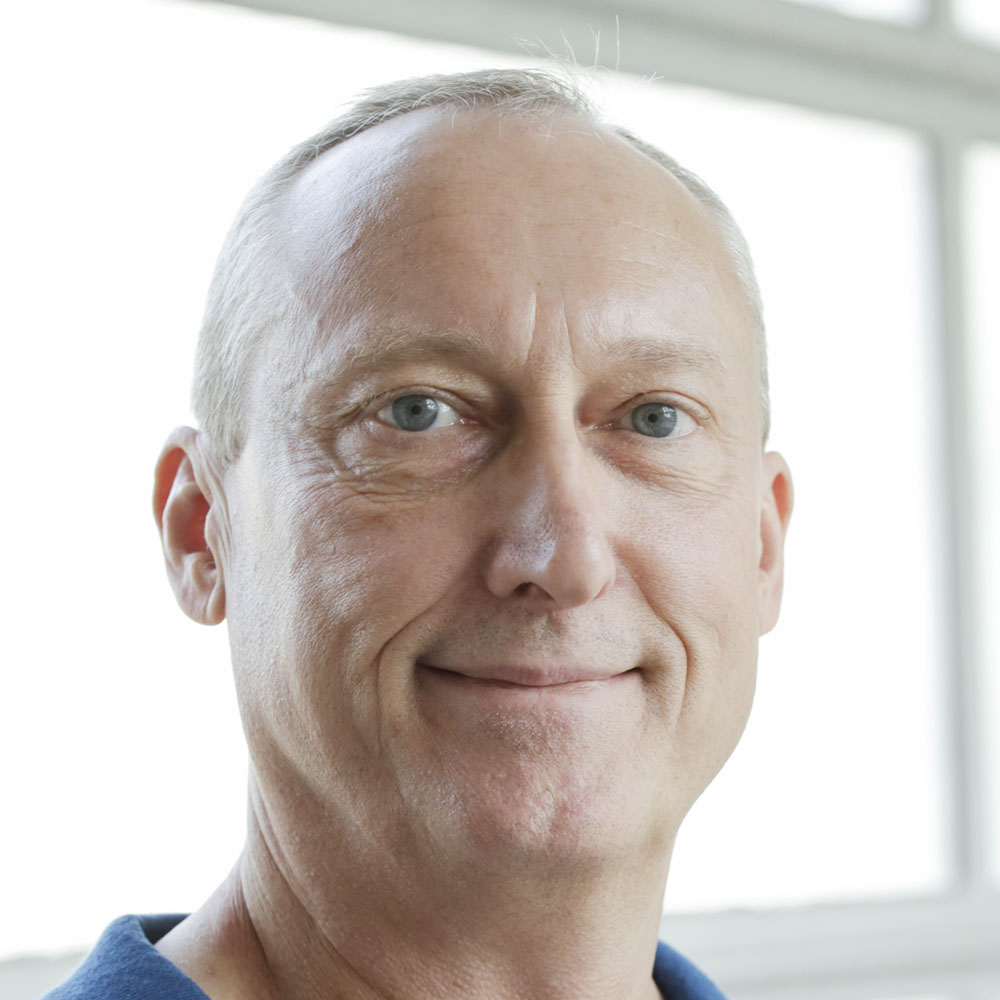
Price excludes tax and duties.
The 6th participant from the same company can join for free.

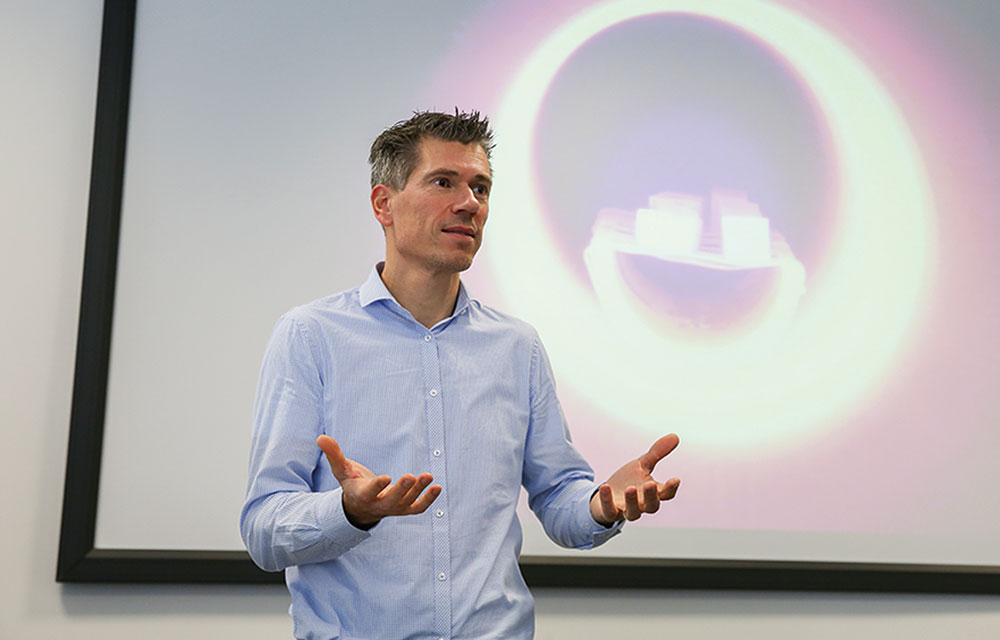
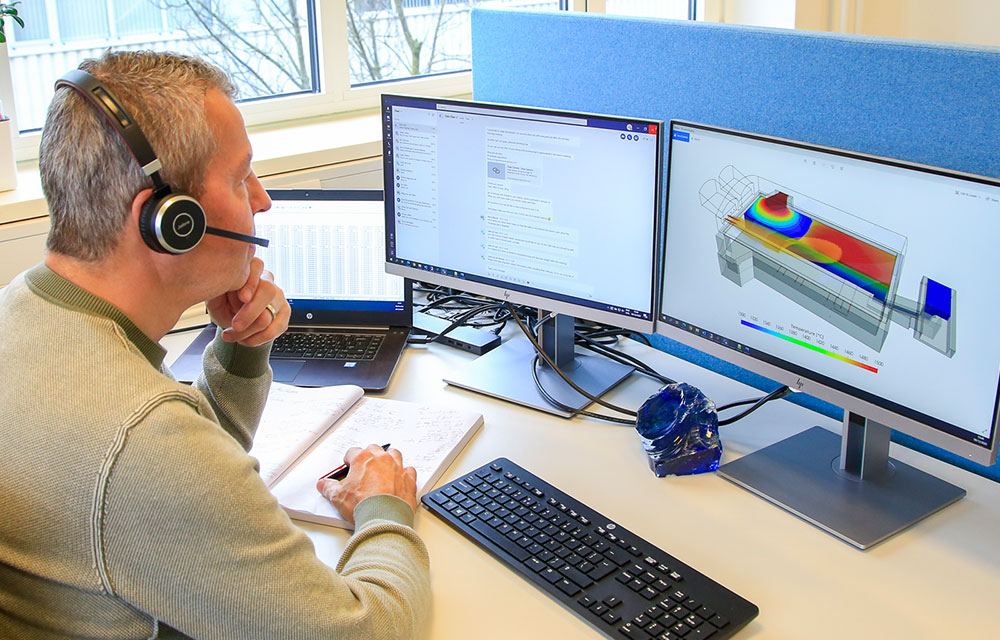

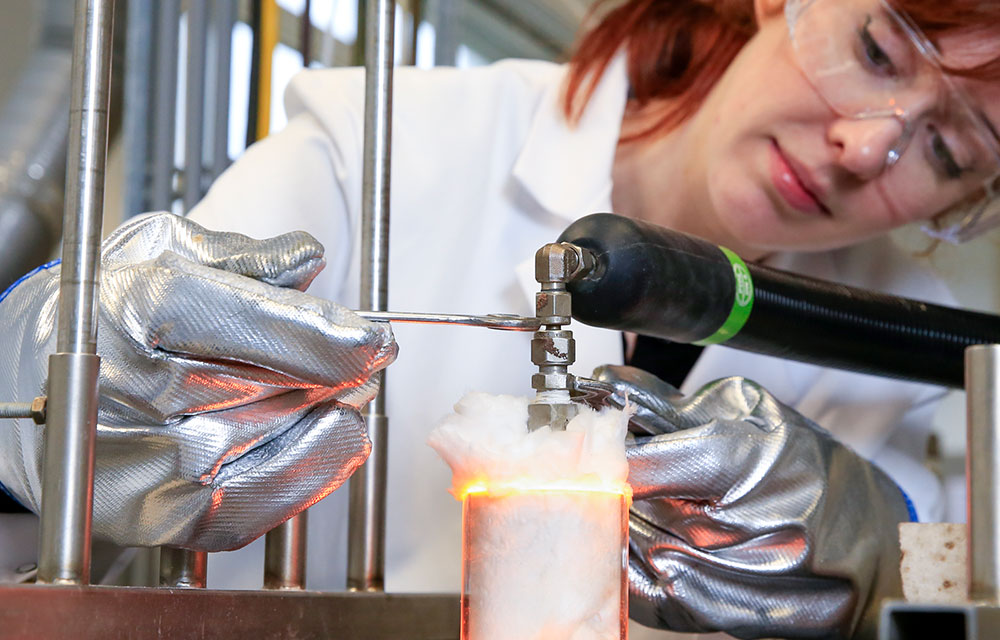
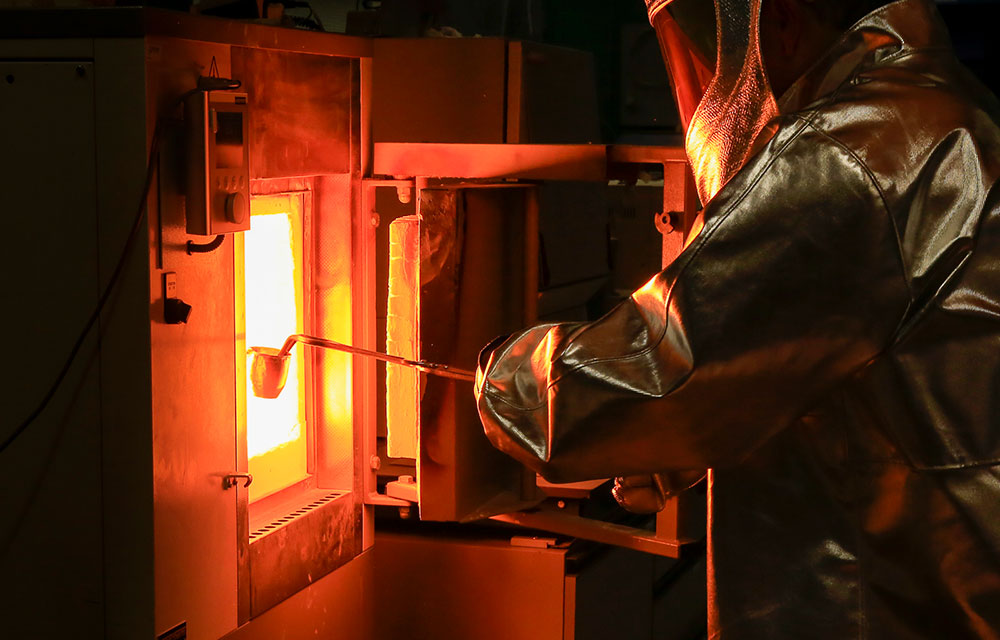
